Blow Moulding Applications
The costs in blow molding are lower as compared to injection molding because machinery costs are typically lower as well. In blow moulding process, one-piece construction is done so that there’s no need to connect part halves, which can achieve shapes that injection molding cannot produce
NEED FOR BLOW MOULDING
TYPES OF BLOW MOULDING
A) Extrusion blow molding(one stage)




B) Injection blow molding (one stage)
C) Injection stretch blow molding (two stages)


Advantages of Using Bajaj Masterbatch for Blow Moulding


Ability to handle complex part


Fast Production Rate


Enhanced Strength


Increases the tensile strength


High level of producivity


Low Costs
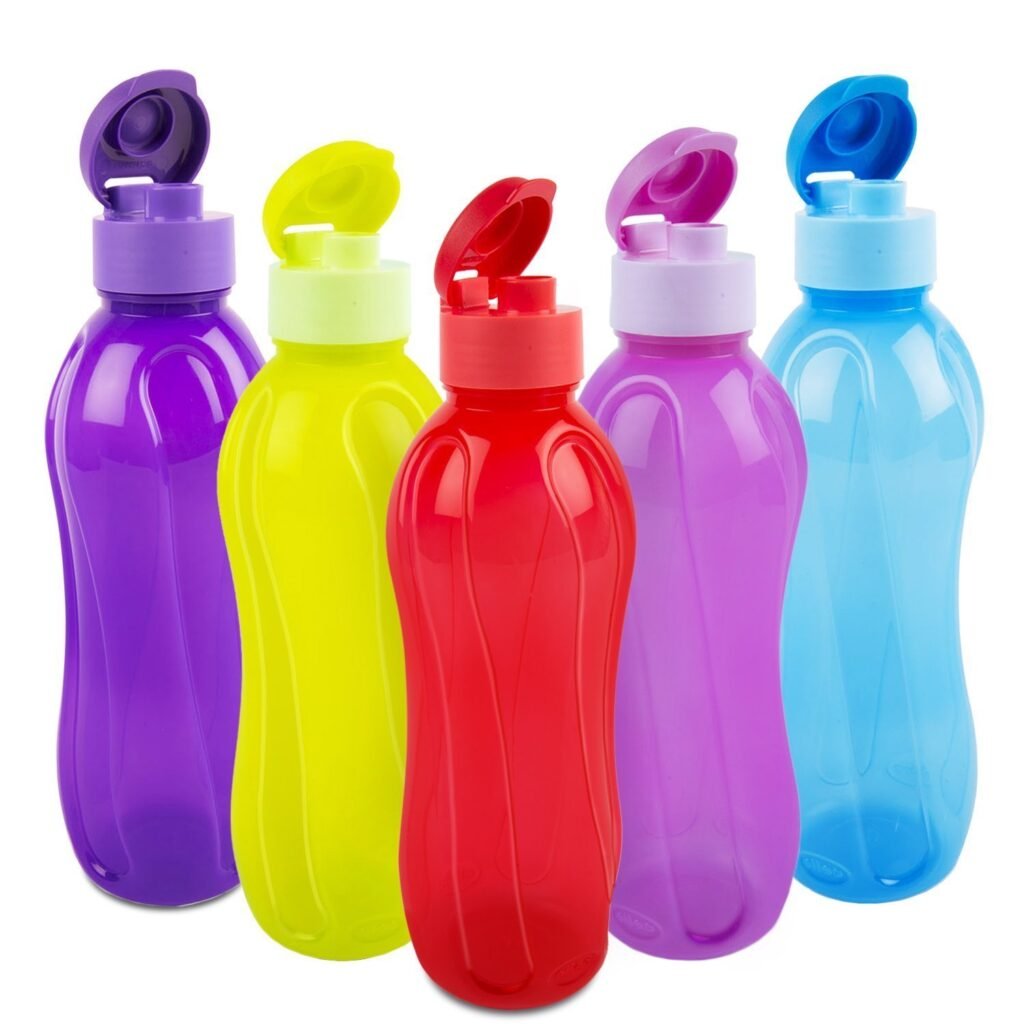
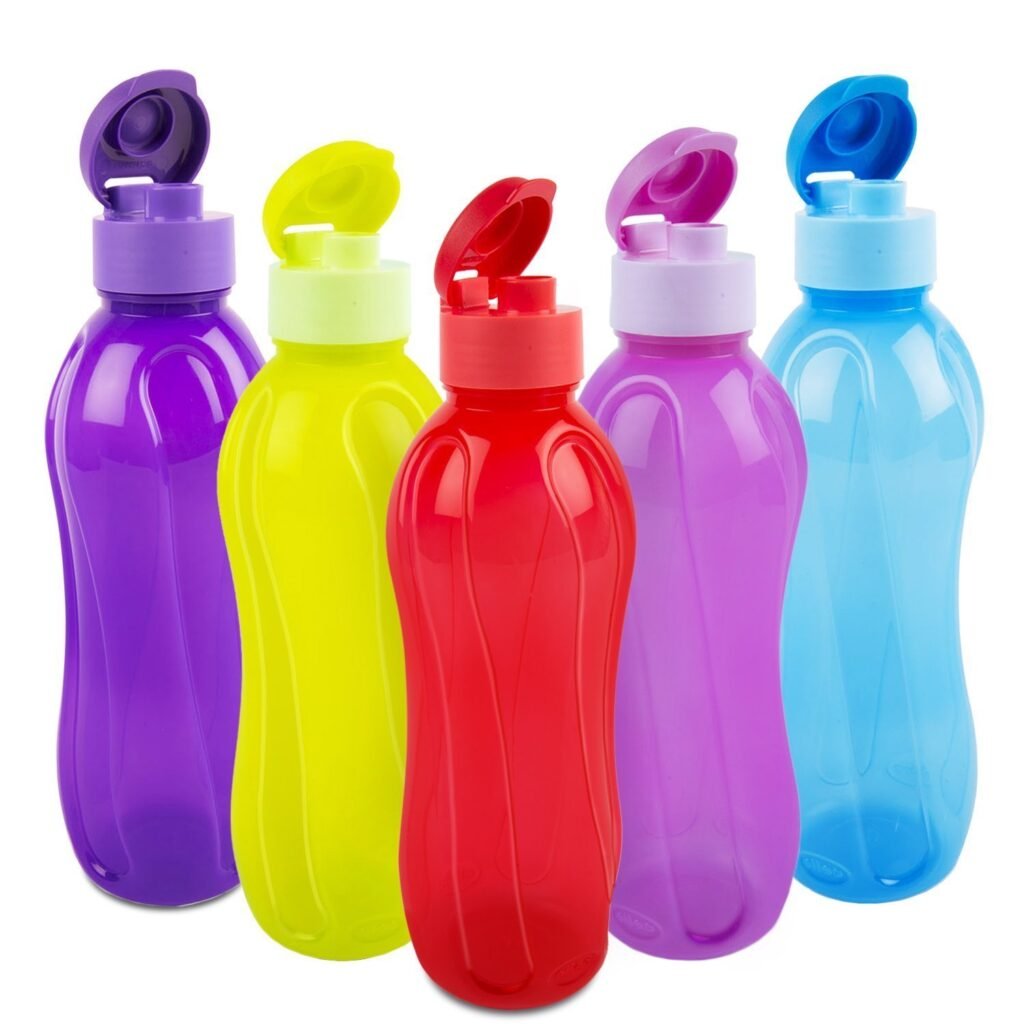
Instead of having pre coloured compounds, usage of our masterbatches facilitates low stock holding as and when required.
Compared to compounds, our masterbatches gives a choice of wide range of colors and other properties besides saving huge cost as the inventory level & space required is very minimal .
Provides “dust free” environment without any health or safety risks in comparision to conventional usage of pigments powders & additives individually.
Optimum dispersion of pigments and additives in our masterbatches facilitates ease of processing. Also, it reduces the cost of purging & flushing .
Elimination of ‘trial and error’ development or formulation work, as this is done already by us ensuring color strength and consistency forever.
Our masterbatches are filler free and they are fairly highly concentrated (in comparison with the target composition), with “let-down ratios” affordable and economical as per the client’s application requirements.




Provides aesthetic appeal with gloss and brightness on the finished product without any surface defects.
As blow moulded bottles, containers, carboys and drums are extensively used in Pharma and Chemical applications, our masterbatches has the ability to maintain the chemical stability of the pigments and other ingredients incorporated in it. This facilitates migration resistant , leaching free and non reactive & ease of using at any conditions.
We use eco friendly pigments which are not harmful to the environment, on request we can provide ROHS (Restriction of Hazardous Substance) compliance.
Ease of consolidation with polymer at any addition levels and has uniform dispersion.
They are suitable for food contact applications as the ingredients used in it are non-toxic , non hazardous and the articles incorporated with our masterbatches are safe for use.
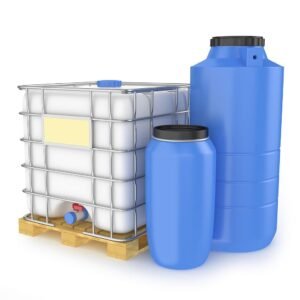
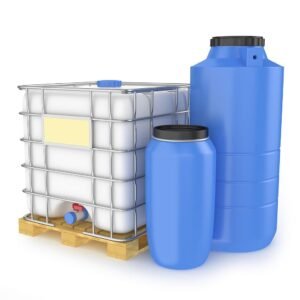
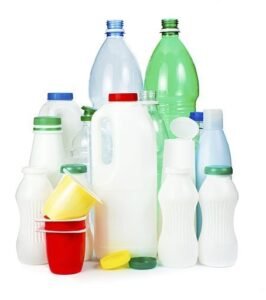
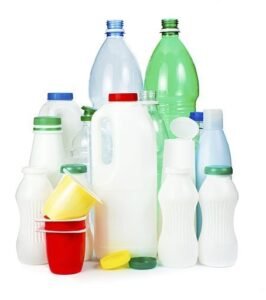
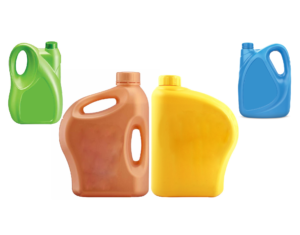
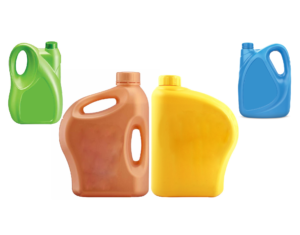
ONE STOP SOLUTION FOR BLOW MOULDING PROBLEMS / DEFECTS
Problems / Defects | Possible Causes | Suggested Remedies |
---|---|---|
Rough crystalline surface | Overheating of co-polymer | 1.Lower the temperature and enhance cooling to certain extent.
Reduce Melt temperature below 200°C
2.Slow down extruder speed. |
Great number of large gels | Overheating of co-polymer in blow moulding machine or grinder | 1.To dismantle head , screw & thoroughly clean.
2.Purging is needed |
Contamination from highly incompatible resins, etc | 1.Some times polymer resins consists of foreign particles
2.Contamination by decomposed particles | 1.Inspect bags, hopper loader, grinder and all other parts wherein polymer is used.
2.Clean die and extruder to evacuate degraded material. 3.Cool the extruder before shut down. |
Pin marks, bubbles or streaks in part | 1.Moisture | Dry resin at 60-70°C for an hour approx. |
Cloudy or hazy part | 1.Contamination
2.Melt temperature too high / low 3.Mould temperature too low | 1.Dry resin at 60-70°C for an hour approx. 2.Adjust Melt temp between180-200°C(approx) 3.Adjust Mold temp between 25-35°C |
Part dull in appearance | 1.Mould is not polished properly.
2.Mold finish is untidy 3.Improper Mould temperature | 1.Do polishing
2.Clean thoroughly and polish with Simichrome 3.Adjust Mould temperature between 25-35°C |
Poor wall thickness distribution from top to bottom | 1.Parison necking down
2.Larger part periphery at top | 1.Parison programming to be done
2.Increase extrusion speed 3.Lower Melt temp 4.Invert mould if possible. |
Poor wall thickness circumferentially | Non symetric part shape | 1..Shape the die to increase parison thickness in thin area. 2.Pre blow parison. 3.Use larger parison diameter. |
Parison rupture or part “Blow out” | 1.Too large a blow up ratio. 2.Mould separation 3.Pinch-off too sharp | 1.Use larger die tooling. 2.Increase clamp pressure / decrease blow pressure 3.Provide wider pinch-off land. |
Die lines | Untidy or damaged die | 1.Clean die land surfaces
2.Nicks or scratches in die or mandrel may have to be removed. 3.Check for foreign material 4.Streamline flow to eliminate die buildup |
Problems/Defects | Possible Causes | Suggested Remedies |
Parison “Doughnut” formation | 1.Mandrel temperature not adequate
2.Mandrel is at too high position. 3.Die face is untidy | 1.Allow mandrel to reach equilibrium with rest of system.
2.Lower Mandrel position slightly 3.Clean the die thoroughly |
Parison length variations | 1.Cooling to extruder feed zone not turned on
2.Insufficient back pressure. 3.Extruder operating erratically. 4.Extruder slipping. | 1.Turn on air / water cooling to feed zone.
2.Increase Back pressure 3.Repair extruder and ensure smooth running. 4.Same as above. |
Low part weight | Wall thickness of parison is too thin | Increase annular opening to make wall thickness to increase slightly. Make parision programming faster. |
Part weight too heavy | 1.Wall thickness of parison is too high | 1.Decrease annular opening to make wall thickness to decrease. |
Part not fully inflated | Blow air pressure inadequate | 1.Increase blow air pressure
2.Check for blocked air lines if any. |
Blow needle not puncturing parison | 1.Insertion rate too slow
2.Needle stroke too short. 3.Needle is blunt | 1.Increase pressure to needle cylinder. 2.Lengthen stroke if possible. Install cylinder with longer stroke. 3.Sharpen needle to ensure good puncture. |
Parison collapses inside mould | Blow air incorrectly timed out | Start blow air earlier in cycle. |
Thinning or stretching at parting line | 1.Low blow pressure
2.Air entrapment inside | 1.Increase blow pressure.
2.Improve mould venting. |
Poor wel at pinch off | 1.Mould temperature high
2.Mould closing speed is fast 3.Pinch off land too sharp | 1.Adjust Mold temp between 25-35°C
2.Increase Mould “Cushion” or decrease mould closing speed. 3.Widen pinch land , Dam up inch-off relief to thicken pinch weld. |
Warpage | 1.Insufficient cooling
2.Non-uniform cooling 3.Cooling differential in thick & thin areas | 1.Provide good water flow in moulded channels
2.Increase cooling time. 3.Improve wall distribution of cooling channel. |
Product Solutions for Blow Moulding


Blow Moulding Applications for
Color Masterbatch
Blow Moulding Applications for
White Masterbatches
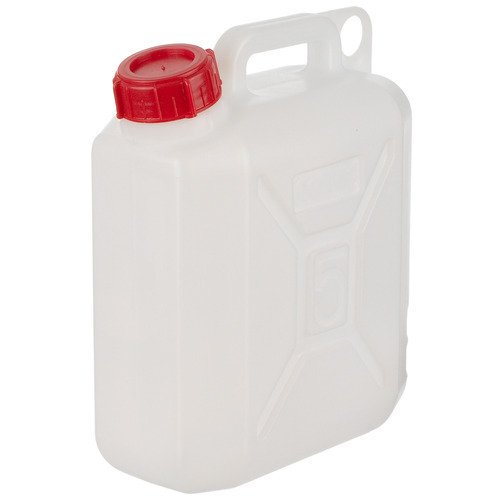
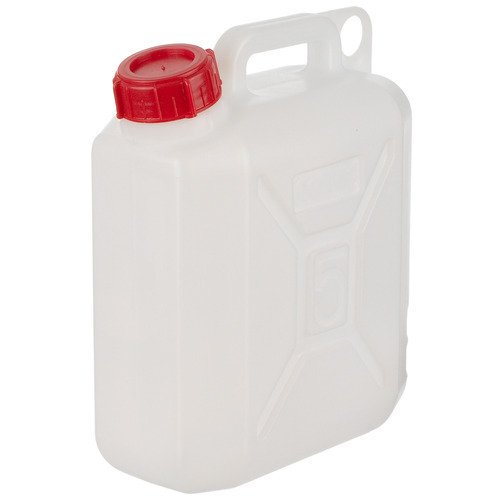


Blow Moulding Applications for
Black Masterbatch
Blow Moulding Applications for
Transparent Masterbatch


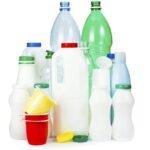
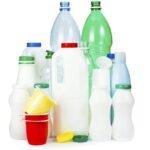












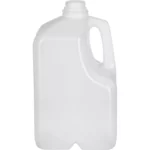
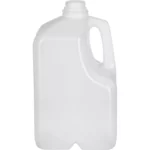



